Gear pumps
SMITH pumps are positive displacement gear pumps. They include a body, a sealing assembly as well as motor and satellite gears.
Balanced Load Configuration: Minimizes gear tooth contact and eliminates constant heat-generating case contact. Enables smooth, pulsation-free flow and higher differential pressures.
Graphite Ball Bearings: These bearings support the full length of the drive shaft. Balanced loading eliminates the need for a duplicate ball bearing at the end of the drive shaft and a second mechanical seal.
Shaft with Superseal packing: the Superseal assembly is mounted as a kit on the pump drive shaft. This allows dynamic pressure testing before assembly into the pump or when supplied as a separate component. The 3-piece seal allows slow rotation of the intermediate seal ring, greatly reducing wear associated with friction.
The gears are easily accessible: without disturbing the mechanical seal, the gear train can be easily replaced.
Maintenance-Free Ball Bearings: Our design eliminates the need for periodic greasing.
Conversion to Larger Capacity Pump: Higher flow rates can easily be achieved with the addition of one, two or three secondary gear cases, each with a flow capacity of 50 GPM.
Principle of operation
Fluid first enters the pump inlet, shown in blue in the upper left corner of the main pump housing. It is also routed inside the pump to the lower right port, also shown in blue through the port in the gear end housing. As the motor pinion in the center rotates counter-clockwise, the low pressure blue fluid is directed into the spaces between the gear teeth and transferred to the red ports as shown.
The speed of the liquid entering the gear tooth gaps is carefully matched to the speed of the gear set to minimize changes in speed and changes in direction of the liquid, thereby minimizing pressure drop across the pump.
The gear housings are designed to ensure that a pressure gradient exists around the outside diameter of the intermediate gears to suppress cavitation and maximize pump transfer rate.
It is the design and efficiency of the non-contact side of the gear teeth (in the red areas) that largely determines the pump’s ability to develop pressure.
The allowable wear on the front side of the gear teeth does not compromise this performance characteristic of the Smith 3-gear pump.
The red ports are also built into the pump (high pressure). It is important from a load perspective that the drive pinion is exposed to a neutral load, eliminating the need for another ball bearing to support the other end of the drive shaft ( which would also add another mechanical seal).
Since the diagram uses color to indicate pressure, the symmetrical colors surrounding the drive sprocket illustrate that this sprocket is balanced.
As high pressure builds in the red ports, fluid maintains velocity and flows out of the pump through the outlet port shown in red in the upper right corner.
Secondary gearboxes can be added to the main gearbox shown and have internal holes to match those of the main gearbox. The addition of a secondary gear housing does not increase the working pressure of the pump, but rather increases its volumetric flow.
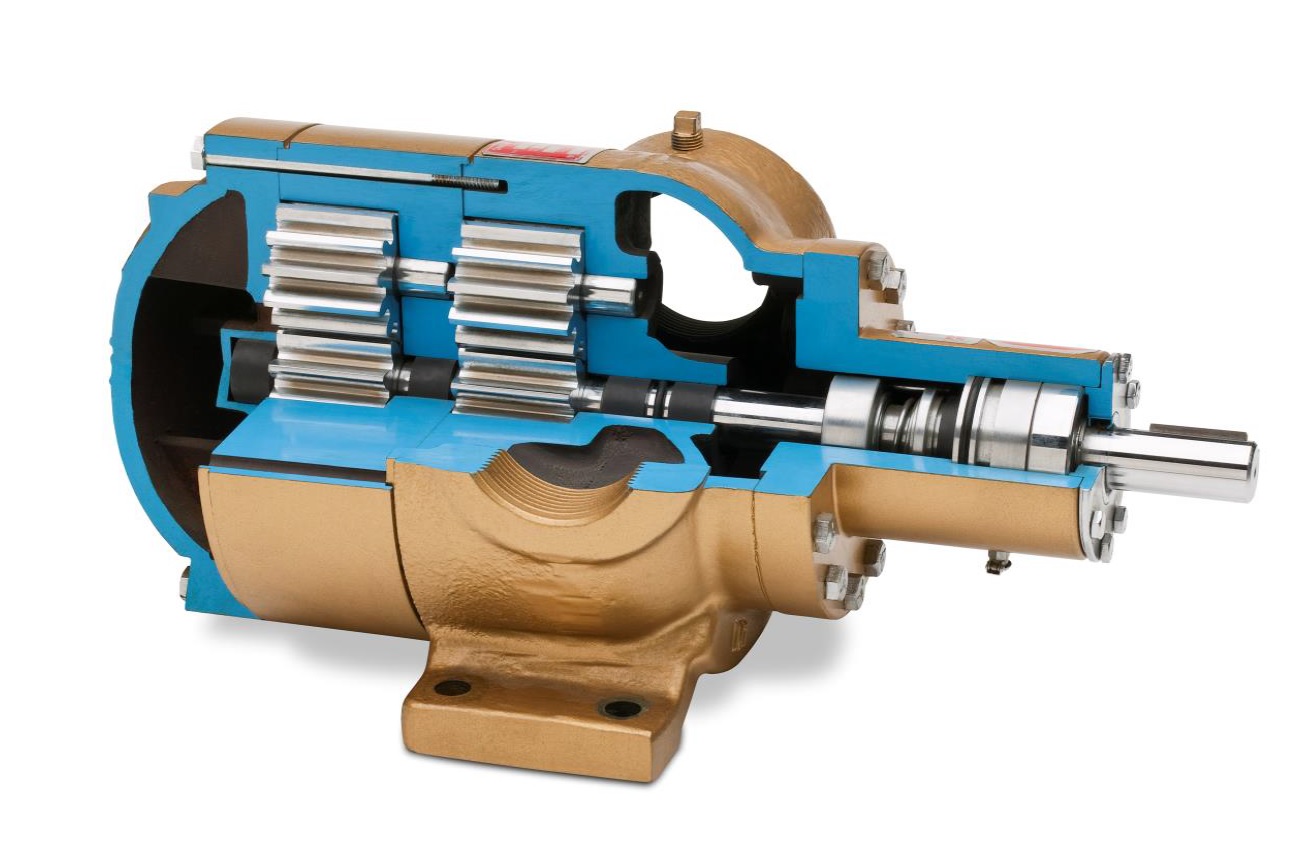
Product categories
This product is present in the following categories: